“If you’re willing to learn, they’re willing to teach you.”
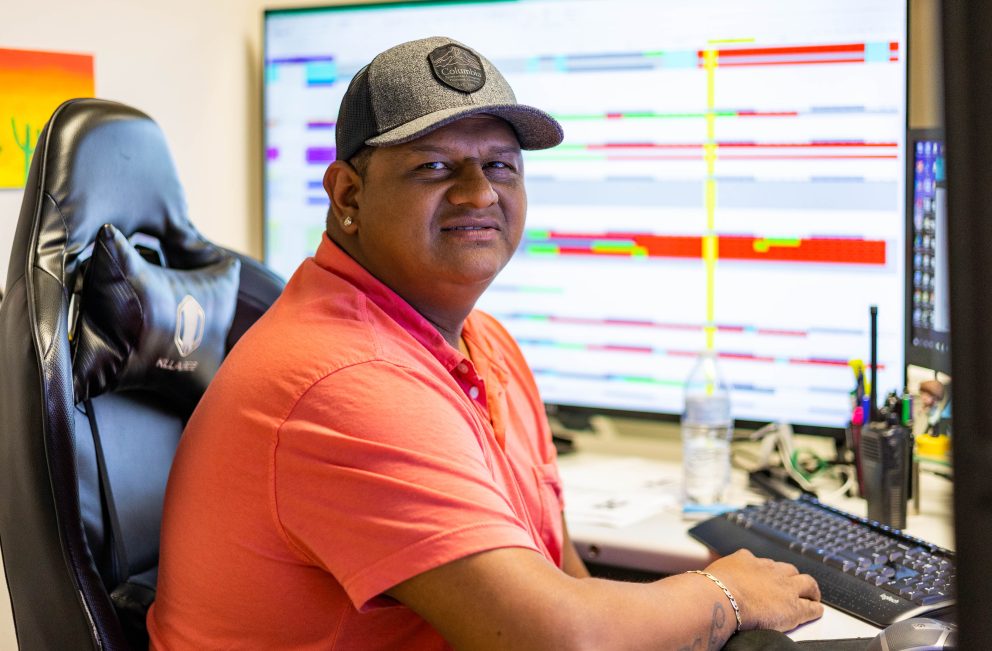
It’s been nearly two decades at Unistress for David Hernandez, who was recruited to the work crew in 2005 by a cousin. He began working in the plant with no manufacturing experience. “I was making pizzas before – this was all new to me.” While he immigrated to the U.S. in second grade, his family frequently spoke Spanish in the home. “When I started as a crew worker, I didn’t know the English names for things. I didn’t know what a tape measure was.” Reflecting on his early days in production, “The guys on the beds all taught me different things. You’re welcomed by everybody here. If you’re willing to learn, they’re willing to teach you.”
During a period of company growth, Unistress was looking for talent who understood the operation as we began to clock each part of our manufacturing process. Hernandez, who had a strong relationship with his supervisor, was asked to build on his years of experience and aptitude for new technology. “They were looking for someone and said to me, ‘We know you’re smart – and you’re good with computers. This could be a great opportunity for you.’” Says Hernandez, “They offered me the job and I excelled.”
Hernandez now runs schedules for the entire plant. “I do all the scheduling for new projects, and coordinate schedules between departments in a timely manner.” Describing the challenges and solutions inherent in the work, “I create the schedule for a job, from forecasting to meeting a customer’s erection schedules.” He’s bullish on how the role allows him personal growth as the company advances. “Unistress has allowed me to learn many different things that I would not have had another chance to learn. I know a lot of different software applications and how to move product around our plant.”
“I’ve done a lot of things here I never thought I’d be doing.” Hernandez approaches even difficult tasks head on, “I love challenges and I’ve been challenged a lot here. I work out complicated schedules and get product made by the date we say we’ll get it done.”